Optimizing Your Welding WPS: Methods for Improved Performance and Performance
Optimizing Your Welding WPS: Methods for Improved Performance and Performance
Blog Article
Unlocking the Power of Welding WPS: Techniques for Effectiveness and Security in Construction
In the realm of construction, Welding Procedure Specifications (WPS) stand as the backbone of welding operations, determining the essential steps for attaining both performance and safety and security in the manufacture procedure. Comprehending the complexities of WPS is critical to utilizing its full possibility, yet several companies have a hard time to unlock the true power that exists within these records (welding WPS). By diving into the techniques that maximize welding WPS, a globe of boosted efficiency and heightened safety waits for those ready to check out the nuances of this vital facet of construction

Relevance of Welding WPS
The value of Welding Procedure Specifications (WPS) in the manufacture market can not be overstated. WPS function as a crucial roadmap that lays out the essential actions to make sure welds are carried out consistently and appropriately. By specifying important criteria such as welding processes, materials, joint layouts, preheat temperatures, interpass temperature levels, filler steels, and post-weld warmth treatment needs, WPS supply a standardized method to welding that boosts performance, high quality, and safety and security in construction processes.
Adherence to WPS helps in attaining uniformity in weld top quality, minimizing the likelihood of issues or structural failings. This standardization also assists in compliance with market regulations and codes, making sure that made structures fulfill the needed safety and security standards. Additionally, WPS documentation allows welders to reproduce successful welding treatments, bring about consistent outcomes throughout different jobs.
Basically, the precise growth and strict adherence to Welding Procedure Specs are extremely important for supporting the stability of bonded structures, securing versus possible risks, and maintaining the online reputation of fabrication business for providing high-grade services and products.
Key Aspects of Welding WPS
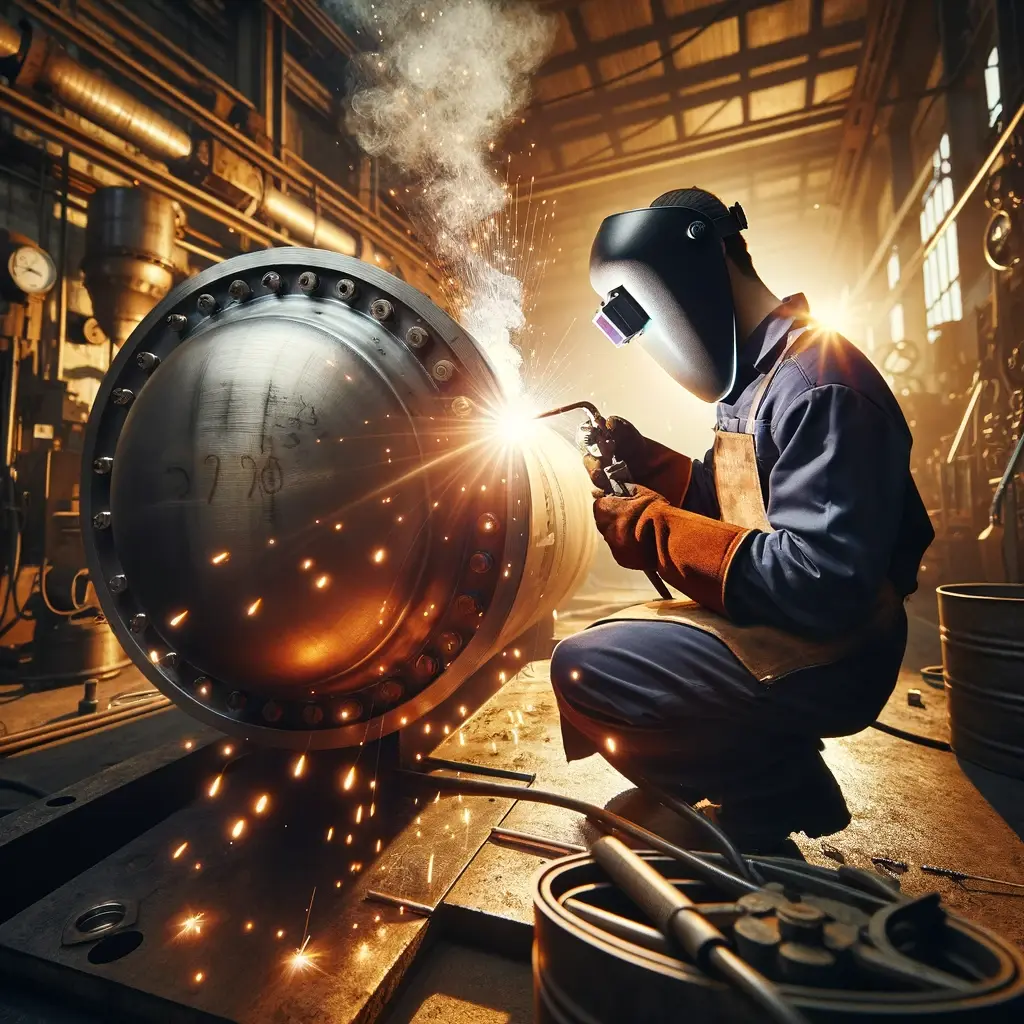
Enhancing Effectiveness With WPS
When maximizing welding operations, leveraging the key elements detailed in Welding Treatment Specifications (WPS) comes to be vital for maximizing and improving processes efficiency. One method to improve performance with WPS is by meticulously picking the appropriate welding parameters. By adhering to the specific standards provided in the WPS, welders can ensure that the welding equipment is established correctly, leading to consistent and top quality welds. In addition, adhering to the pre-approved welding series outlined in the WPS can significantly decrease the moment invested on each weld, ultimately boosting overall productivity.
Frequently assessing and updating the WPS to integrate any kind of lessons learned or technical advancements can likewise add to performance improvements in welding procedures. By welcoming the guidelines established forth in the WPS and continually seeking address methods to maximize procedures, fabricators can accomplish greater performance levels and exceptional end outcomes.
Ensuring Safety in Manufacture
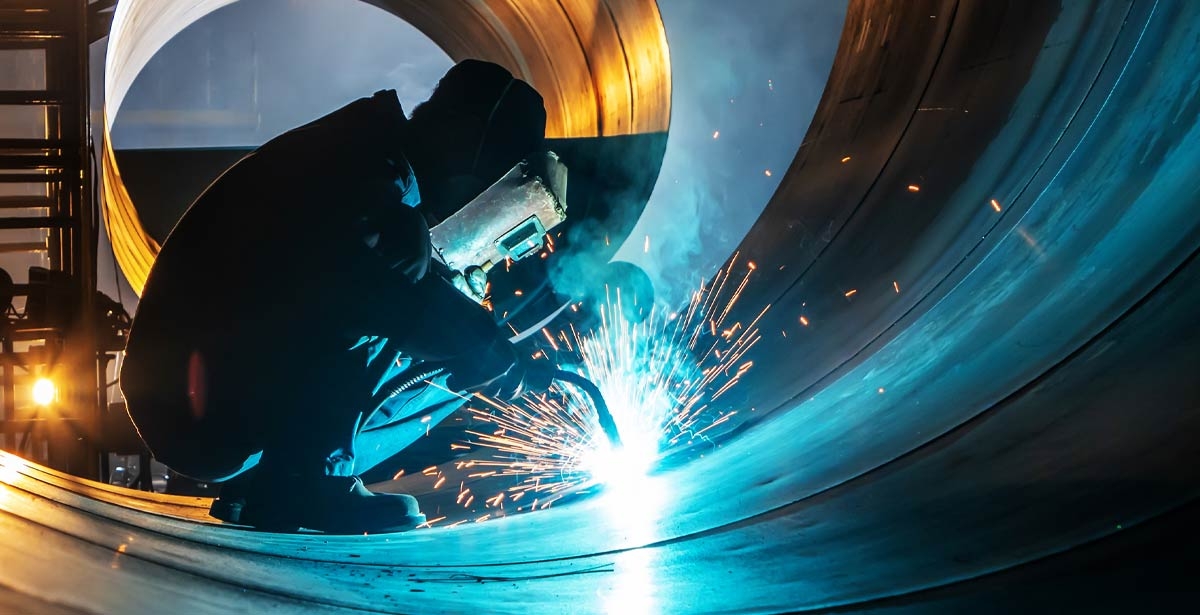
Safety protocols in fabrication play a pivotal role in safeguarding employees and maximizing functional procedures. Guaranteeing security in fabrication involves a complex strategy that incorporates different aspects of the welding process. One basic facet is the arrangement of personal safety tools (PPE) customized to the certain threats existing in the manufacture atmosphere. Welders should be equipped with ideal equipment such as safety helmets, gloves, and safety garments to mitigate threats connected with welding activities.
Moreover, click here to find out more adherence to proper ventilation and fume extraction systems is vital in preserving a healthy and balanced work environment. Welding fumes consist of hazardous materials that, if inhaled, can posture major wellness risks. Carrying out effective air flow measures assists to decrease exposure to these unsafe fumes, promoting respiratory system health amongst employees.
Regular devices upkeep and evaluations are likewise essential for making sure safety and security in fabrication. Malfunctioning equipment can result in injuries and accidents, highlighting the importance of routine checks and prompt repair work. By prioritizing precaution and cultivating a culture of awareness, construction centers can develop a secure and efficient workplace for their personnel.
Executing WPS Finest Practices
To improve operational performance and make certain quality end results in manufacture procedures, including Welding Treatment Spec (WPS) best methods is paramount. Picking the suitable welding procedure, filler material, and preheat temperature specified in the WPS is vital for achieving the wanted weld quality. Making certain that qualified welders with the needed accreditations bring out the welding treatments according to the WPS guidelines is vital for consistency and dependability.
Conclusion
To conclude, welding WPS plays a crucial function in making certain efficiency and security in manufacture processes. By click here now concentrating on vital elements, improving performance, and implementing finest techniques, companies can enhance their welding procedures. It is vital to prioritize security actions to avoid mishaps and make sure a smooth manufacturing process. By following these techniques, services can open the full capacity of welding WPS in their manufacture procedures.
In the world of manufacture, Welding Treatment Requirements (WPS) stand as the foundation of welding procedures, determining the needed actions for accomplishing both effectiveness and security in the construction process. By specifying crucial parameters such as welding procedures, products, joint styles, preheat temperatures, interpass temperature levels, filler steels, and post-weld warmth treatment requirements, WPS offer a standard technique to welding that improves effectiveness, quality, and safety in fabrication procedures.

When maximizing welding operations, leveraging the crucial elements detailed in Welding Procedure Specs (WPS) comes to be essential for enhancing procedures and taking full advantage of performance. (welding WPS)
Report this page